3D Printing Colloidal Probe AFM
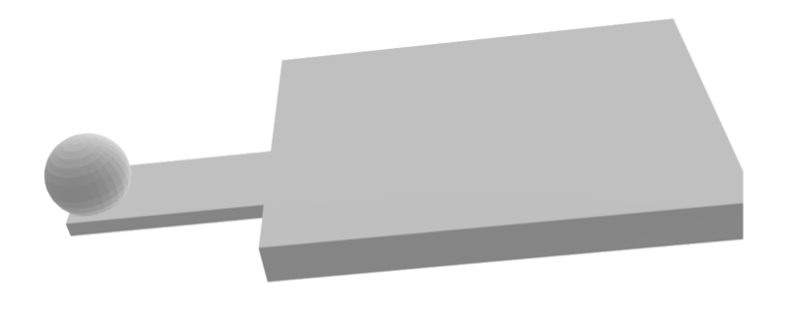
Atomic force microscopy (AFM) is a crucial tool for characterizing surfaces at the nanoscale, widely used in research and industry. The performance of an AFM heavily relies on the quality and design of its cantilever, which directly interacts with the sample surface. Traditional fabrication methods such as photolithography and etching, have limitations in achieving the intricate designs and desired feature sizes of colloidal probe needed for force spectroscopy and friction measurments.
This project aims to leverage the precision of two-photon lithography to design and fabricate colloidal probe AFM cantilevers. By utilizing two-photon lithography, we can achieve nanoscale resolution and complex geometries that traditional manufacturing methods cannot accomplish, thus enhancing the performance and versatility of AFM colloidal probes for various applications in materials science, life science and in nanotribology.
3D printing using two-photon lithography allows the fabrication of structures with sub-micron resolution by utilizing a nonlinear optical process. This method involves the simultaneous absorption of two photons, leading to polymerization only at the focal point of a laser beam, thus enabling the creation of highly detailed 3D structures.
Description:
1. Design AFM cantilevers with optimized geometries for applications in force spectroscopy and friction measurements.
2. Fabricate these designs using two-photon lithography to achieve superior precision and structural complexity of colloidal probes.
3. Characterize the mechanical properties and performance of the fabricated probes.
4. Compare the performance of probes with those made using conventional methods.
Goal:
1. Design:
o Utilize CAD software to create models of AFM cantilevers with varied shapes, sizes, and tip geometries.
2. Fabrication:
o Employ a commercial nanoscribe 3D printer to print the designed cantilevers.
o Optimize the printing parameters to achieve high resolution and structural integrity.
3. Characterization:
o Use scanning electron microscopy (SEM) and atomic force microscopy (AFM) to inspect the fabricated cantilever dimensions and quality.
o Measure resonance frequency, quality factors and stiffness of printed cantilvers.
4. Performance Evaluation:
o Test the cantilevers in various AFM applications mostly friction and adhesion force measurments.
o Compare the performance its normal and lateral force sensitivities with commercially available cantilevers.
Contact details:
Dr. Shivaprakash Narve Ramakrishna, Laboratory for Soft Materials and Interfaces, Department of Materials, ETH Zürich.
If you are interested, please send an email with a short motivational letter to